แก้ไขปัญหาจุดรั่วบนชุดประตูรถ
Scanning and Inspection Pty หันมาใช้ PolyWorks® และวิเคราะห์ความสัมพันธ์ระหว่างกรอบประตูกับตัวถังรถได้ในเวลาไม่ถึง 1 ชั่วโมง
ผู้ผลิตทราบดีว่า เมื่อมีบางสิ่งผิดปกติเกิดขึ้น การค้นหาสาเหตุมักเป็นงานที่ต้องใช้กระบวนการเข้ามาเกี่ยวข้องมากขึ้น และการตรวจสอบที่ตามมาต้องใช้ทั้งเวลา เงินทอง และทรัพยากร แม้จะพบปัญหาในที่สุด แต่ก็ต้องทำการปรับเชิงปริมาณ ซึ่งก็เป็นอีกขั้นตอนหนึ่งที่นำไปสู่การแก้ไข บางครั้งชิ้นส่วนที่ผลิตได้นั้นแตกต่างจากชิ้นส่วนที่ออกแบบมา หรือแตกต่างจากที่ควรจะเป็นหรือเคยเป็นในอดีต คำถามก็คือ แตกต่างกันแค่ไหน ตรงไหน และในทิศทางใด สำหรับผู้ผลิตรถยนต์สัญชาติออสเตรเลียรายใหญ่ การระบุสาเหตุจุดรั่วที่ชุดประตูเป็นปัญหาสำคัญยิ่ง

ModelMaker Z70 ติดตั้งบน FaroArm
ความท้าทาย
ผู้ผลิตยานยนต์รายหนึ่งเพิ่งประสบกับหนึ่งในปัญหาการผลิตที่หลีกเลี่ยงไม่ได้ พวกเขาพบการผันแปรในการวางแนวซีลประตูห้องโดยสารที่พวกเขาผลิตและประกอบขึ้นมา ซึ่งปรากฏว่ารถยนต์ที่ผลิตขึ้นมาในช่วงหนึ่งของการผลิตเป็นไปตามที่คาดโดยที่ประตูและซีลสบกับตัวถังรถที่เหลือได้พอดีอย่างไร้ที่ติ แต่รถยนต์ที่ออกมาจากสายการผลิตในช่วงหลังพบปัญหาน้ำรั่วระหว่างขั้นการทดสอบ งานแรกคือการค้นหาว่าน้ำเข้ามาจากที่ไหน แต่การวิเคราะห์เพิ่มเติมนั้นจำเป็นต้องหาความสัมพันธ์ระหว่างกรอบประตูกับตัวถังรถด้วย ทว่าการหาความแตกต่างจากรถที่ไม่มีปัญหาน้ำรั่ว และประเมินว่ามีความแตกต่างมากแค่ไหน ตรงไหน และทิศทางใด ถือเป็นความท้าทายทีเดียว
หากรถยนต์ชุดหนึ่งออกมาจากสายการผลิตโดยไม่มีปัญหาน้ำรั่ว แต่รถยนต์ชุดอื่น ๆ ที่ผลิตในช่วงหลังเกิดการรั่วแล้วละก็ แสดงว่าโครงสร้างของรถยนต์ต้องมีความแตกต่างอะไรสักอย่าง แล้วชุดกรอบประตูที่เป็นปัญหาแตกต่างจากชุดกรอบประตูของ 'รถยนต์ที่ดี' อย่างไร เพื่อหาคำตอบว่าต้องปรับเปลี่ยนอย่างไรบ้างในขั้นตอนการผลิต ลูกค้าจึงต้องหาปริมาณความคลาดเคลื่อน รวมทั้งจำเป็นต้องประเมินความสัมพันธ์และความแปรผันระหว่างชุดกรอบประตูที่ 'ดี' และ 'ไม่ดี' ด้วย และด้วยเทคโนโลยีการสแกนเลเซอร์แบบใหม่ล่าสุดและชุดโปรแกรม PolyWorks® บริษัทจึงได้ผลลัพธ์การวิเคราะห์เปรียบเทียบอย่างละเอียดในเวลาไม่ถึงชั่วโมง
โซลูชัน
การเก็บข้อมูล
ผู้เชี่ยวชาญที่ Scanning and Inspection ใช้เครื่องสแกนเลเซอร์ที่ติดตั้งอยู่บนแขนข้อต่อ เพื่อใช้เก็บข้อมูลพื้นผิวอย่างรวดเร็วและมีประสิทธิภาพ เครื่องสแกนเลเซอร์ที่นำมาใช้ในงานนี้คือ ModelMaker Z70 ซึ่งเป็นเครื่องสแกนคุณภาพสูงที่สามารถแปลงข้อมูลพื้นผิวเป็นดิจิทัลได้อย่างน่าประทับด้วยความหนาแน่น 0.05 มม. x 0.05 มม. หรือประมาณ 400 จุดต่อตารางมิลลิเมตร การเก็บข้อมูลนี้ได้ผลลัพธ์เป็นข้อมูลดิจิทัล 3 มิติสมจริงตามขนาดจริงของชิ้นส่วน ซึ่งเป็นข้อมูลมากมายที่รอให้แปลงเป็นข้อมูลที่เป็นประโยชน์ เครื่องสแกนรับจุดอ้างอิง 3 มิติจาก CMM พกพา ซึ่งในกรณีนี้คือ Platinum FaroArm ซึ่งวัดการทำซ้ำได้ตั้งแต่ ±0.0051 มม. ขึ้นไป ขึ้นอยู่กับขนาด FaroArm และเครื่องสแกนเลเซอร์ MMZ70 ถูกเข็นเข้าตำแหน่งบนขาตั้งแบบ 3 ขาสำหรับงานหนัก จึงสามารถตั้งฮาร์ดแวร์ติดกับประตูรถยนต์ที่ต้องการได้อย่างสะดวกสบาย ซึ่งการจับข้อมูลพื้นผิวที่ต้องการใช้เวลาไม่กี่นาทีเท่านั้นสำหรับรถแต่ละคัน
กระบวนการของ PolyWorks
เมื่อรวบรวมข้อมูลการสแกนได้แล้ว ขั้นตอนวิเคราะห์หลังการประมวลผลก็จะเริ่มขึ้น ผู้เชี่ยวชาญที่ Scanning and Inspection Pty Ltd. ใช้ PolyWorks วางแนวข้อมูลสแกนด้วยเลเซอร์ที่ได้จากรถ "ที่มีรอยรั่ว" เข้ากับรถ "ที่ดี" ภายในระบบเสมือน จากนั้นจึงทำการวิเคราะห์การวัดและเปรียบเทียบขั้นสูง อย่างไรก็ตาม ก่อนการวิเคราะห์เปรียบเทียบ จะต้องมีการปรับเปลี่ยนพอยต์คลาวด์จำนวนหนึ่งใน PolyWorks ด้วย
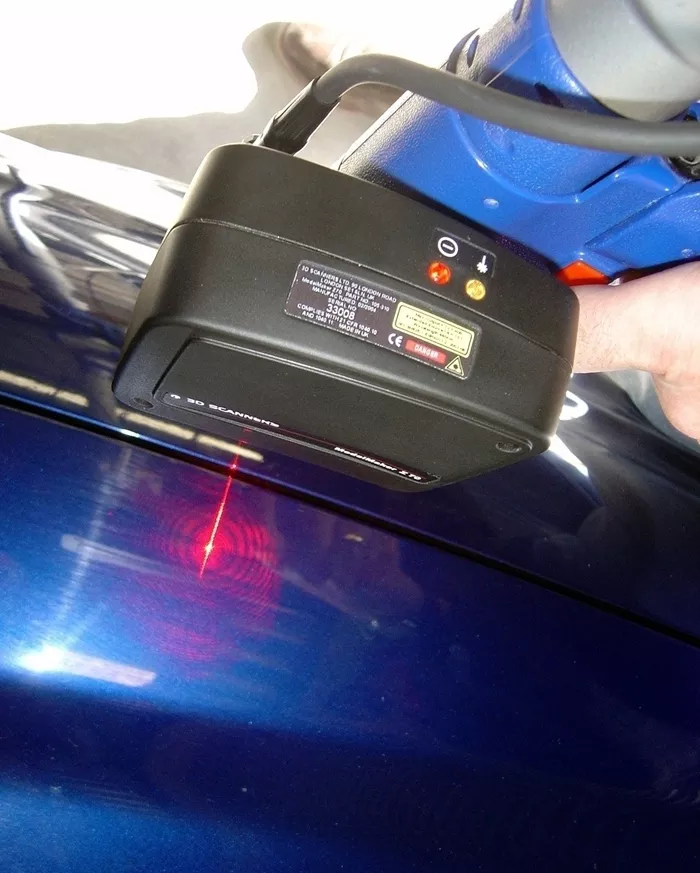
การเก็บข้อมูล
การปรับการวางแนวการสแกนอย่างละเอียด
การเก็บข้อมูลจะต้องอาศัยการสแกนผ่านหลายครั้ง แถบการสแกนแต่ละส่วนจะถูกวางเรียงกันโดยอัตโนมัติ โดยใช้เทคโนโลยีการวางแนวของแขนข้อต่อ ซึ่งให้การอ้างอิงเชิงพื้นที่สำหรับตำแหน่งที่เปลี่ยนแปลงไปของเครื่องสแกนเลเซอร์ พอยต์คลาวด์ส่วนใหญ่ที่ได้จากเครื่องสแกนเลเซอร์จะ "วาง" ทับจุดอื่นที่เครื่องสแกนได้สแกนผ่านมาแล้ว ผลก็คือบางส่วนของชิ้นส่วนถูกวัดมากกว่าหนึ่งครั้ง พื้นที่เหล่านี้จะมีข้อมูลหลายชั้น ซึ่งเรียกว่าพื้นที่ซ้อนทับ
ดังนั้นเพื่อปรับพอยต์คลาวด์ที่วางแนวแล้ว ซึ่งได้มาจาก CMM พกพา โมดูล PolyWorks IMAlign จะใช้พื้นที่ซ้อนทับเหล่านี้ในการจัดเรียงการสแกนทั้งหมด ในขั้นแรก จะมีการวิเคราะห์การเบี่ยงเบนกับพอยต์คลาวด์ที่วางแนวแล้ว PolyWorks จะคำนวนระยะห่างโดยเฉลี่ยระหว่างการสแกนที่ซ้อนทับกันแต่ละจุดให้โดยอัตโนมัติ และแสดงสีที่ใช้แทนค่าเบี่ยงเบน แค่มองผ่าน ๆ ผู้ใช้ก็จะมองเห็นการสแกนที่อยู่นอกค่าความคลาดเคลื่อนยินยอมได้ และสามารถปรับปรุงได้โดยการเรียงแนวใหม่
จากนั้นจึงใช้เทคโนโลยีการวางแนว "Best-fit" ของ PolyWorks ในการวางแนวใหม่ เพื่อป้องกันไม่ให้เกิด "การเลื่อน" ระหว่างแต่ละแถบในพื้นที่เดียวกัน การสแกนแต่ละครั้งจะมีการกำหนดจุดควบคุม 8 จุดโดยอัตโนมัติ ซึ่งจะจำกัดระดับความเป็นอิสร คุณสมบัตินี้ทำให้ PolyWorks แตกต่างจากโซลูชันการวางแนวการสแกนอื่น ๆ ซึ่งมักพบปัญหาการเลื่อนในระหว่างการวางแนวการสแกน หลังจากวางแนว Best-fit แบบจำกัดความเป็นอิสระแล้ว จะมีการคำนวณการวิเคราะห์ความเบี่ยงเบนใหม่ และแสดงผลแผนที่สี
ขั้นตอนสุดท้ายประกอบด้วยการสร้างแบบจำลองพอยต์คลาวด์ชั้นเดียว โดยการเฉลี่ยการสแกนที่ซ้อนทับกันทั้งหมดอย่างชาญฉลาด โดยใช้เทคโนโลยี "ลดการซ้อนทับ" ของ PolyWorks ในตอนนี้ พอยต์คลาวด์ที่ได้จะสามารถแปลงเป็นพื้นผิวที่สามารถใช้สำหรับการวิเคราะห์ต่อไป เช่น การเปรียบเทียบประตู เป็นต้น ขั้นตอนการสแกนนั้นเหมือนกันทั้งสำหรับรถ 'ที่รั่ว' และรถ 'ที่ดี' ขอบรอบทั้งหมดถูกลบจากกรอบหน้าต่างและกรอบประตู เพื่อเผยให้เห็นเฉพาะโครงสร้างส่วนประกอบเหล็กหลังการผลิตเท่านั้น ประตูปิดไว้ตลอดกระบวนการเก็บข้อมูล และบริเวณที่เกี่ยวข้องกับซีลที่รั่วจะได้รับการสแกนโดยใช้เลเซอร์ MMZ70
ระหว่างที่แถบเลเซอร์เลื่อนไปตามพื้นผิว จะมีการเก็บข้อมูลจุด 3 มิติหลายหมื่นจุดต่อวินาที และได้ผลลัพธ์พื้นผิวทันทีบนหน้าจอคอมพิวเตอร์ ความสามารถของการแสดงผลพื้นผิวพอยต์คลาวด์แบบเรียลไทม์ หมายความว่า ผู้ใช้จะเห็นบริเวณที่ขาดไปหรือยังต้องสแกนเพิ่มเติมได้ในขณะวัด และดำเนินการต่อได้ทันที

การสร้างแบบจำลองโพลิกอน
การสร้างแบบจำลองโพลิกอน
เพื่อเปรียบเทียบพื้นผิวชุดกรอบประตู "ที่ดี" และ "ที่ไม่ดี" Scanning and Inspection จำเป็นต้องแปลงพอยต์คลาวด์เป็นสิ่งที่ใช้เป็นพื้นผิว ซึ่ง PolyWorks แปลงจุดหลายหมื่นจุดจากพอยต์คลาวด์เป็นตาข่ายที่ประกอบจากสามเหลี่ยมได้ในพริบตา โดยซอฟต์แวร์ใช้แต่ละจุดเป็นหลักสำหรับสามเหลี่ยมหลายล้านชิ้นที่สร้างขึ้น
เพื่อแสดงภาพรูปทรงต่าง ๆ ของวัตถุที่สแกนได้อย่างเที่ยงตรง PolyWorks ใช้สามเหลี่ยมน้อยลงในส่วนที่มีความสม่ำเสมอมากกว่าส่วนอื่น ๆ บนพื้นผิวของรถ และใช้สามเหลี่ยมมากขึ้นเมื่อเค้าโครงมีความซับซ้อน ซึ่งทั้งหมดนี้อ้างอิงจากค่าความคลาดเคลื่อนยินยอมที่ผู้ใช้กำหนด นอกจากนี้ พารามิเตอร์บริเวณที่ใกล้ที่สุดและระยะห่างการค้นหายังได้รับการกำหนดก่อนการแปลงข้อมูลและการสร้างพื้นผิวสามเหลี่ยม และลดการรบกวนดิจิทัลให้ได้มากที่สุด
การเปรียบเทียบประตู
เมื่อใช้หลักการทางคณิตศาสตร์ "กำลังสองน้อยที่สุด" และการวิเคราะห์พื้นผิว ชุดข้อมูลการสแกนเลเซอร์ที่เป็นสามเหลี่ยมและปรับความเหมาะสมแล้วสองชุดจึงสามารถนำมาซ้อนทับและเรียงกันได้โดยใช้เทคโนโลยีการวางแนว Best-fit ของ PolyWorks จากนั้น PolyWorks จะสร้างรูปแบบการกระจายตามรหัสสีที่เน้นให้เห็นการเปรียบเทียบของชุดประกอบ 2 ชุด แผนที่แสดงข้อผิดพลาดด้วยสีที่ได้มาทำให้สามารถแยกแยะรูปแบบได้อย่างง่ายดาย ซึ่งทำให้เห็นได้ว่าประตูของรถ "ที่ไม่ดี" และมีรอยรั่วแตกต่างจากประตูรถ "ที่ดี" อย่างไร
แกน B และส่วนล่างของประตูแสดงเป็นสีเขียวอ่อน (เกือบอมน้ำเงิน) ซึ่งแสดงว่ามีการเบี่ยงเบนไม่ถึง ±0.5 มม. ระหว่างประตูทั้ง 2 ชุด บริเวณอื่น ๆ เช่น กรอบหน้าต่างเหล็ก ซึ่งเชื่อมกับประตู แสดงเป็นสีเขียว ซึ่งเท่ากับความเบี่ยงเบน ±1-2 มม. สุดท้าย ส่วนสีส้มที่อยู่บนแชสซีของรถก็ระบุความเบี่ยงเบน ±1-2 มม. เช่นกัน
กล่าวอีกนัยหนึ่งก็คือ เมื่อแกน B ของรถทั้งสองคันเรียงกันภายใน 0.5 มม. กรอบหน้าต่างของรถที่รั่วที่จริงแล้วอยู่ในตำแหน่งต่ำกว่ากรอบหน้าต่างของรถที่ไม่มีการรั่ว 0.5 มม. และ 2 มม. ซึ่งเป็นช่องว่างมากพอให้น้ำผ่านเข้ามาได้
คุณประโยชน์
วิศวกรจาก Scanning and Inspection พบว่าการปรับเปลี่ยนการเชื่อมที่เกี่ยวข้องกับตำแหน่งกรอบประตูนั้นทำได้ง่ายกว่าการปรับแชสซีมาก ดังนั้นจึงปรับการเชื่อมบริเวณที่กรอบหน้าต่างสบกับประตู เพื่อให้กรอบไม่ตกลงมาต่ำเกินไป (เทียบกับประตูที่ไม่รั่ว)
กระบวนการตรวจวัดของ PolyWorks ทั้งหมดใช้เวลาไม่ถึง 1 ชั่วโมง
ข้อสรุปที่ได้จากการตรวจสอบมุ่งเน้นที่ข้อกังวลของลูกค้าเกี่ยวกับกรอบหน้าต่างของรถยนต์ หรือที่เจาะจงกว่านั้นก็คือลักษณะการเชื่อมเข้ากับชุดประตูหลัก กระบวนการเชื่อมได้รับการปรับให้เหมาะสม เพื่อให้กรอบหน้าต่างไม่วางห่างเกินไปจากตำแหน่งที่เหมาะสม ตามที่แสดงไว้ในการออกแบบ CAD ขั้นต้น
ความแม่นยำและความยืดหยุ่นของ FaroArm และเครื่องสแกนเลเซอร์ MMZ70 ที่ใช้ร่วมกับซอฟต์แวร์ระดับโลก PolyWorks ช่วยให้ผู้ผลิตรถยนต์รายนี้:
- พบที่มาของปัญหาจุดรั่วได้อย่างรวดเร็ว
- วัดการเบี่ยงเบนทางกายภาพของชุดประตูรถ "ที่ไม่ดี" เปรียบเทียบกับประตูรถ "ที่ดี" ได้อย่างแม่นยำ (เบี่ยงเบนเท่าไหร่ ที่ไหน และทิศทางใด)
- แก้ไขกระบวนการประกอบ โดยการปรับการเชื่อมในจุดที่กรอบประตูสบกับประตู
- ทำกระบวนการตรวจสอบทั้งหมดได้ในเวลาไม่ถึง 1 ชั่วโมง