MetalMan Reduces Inspection Time and Enhances Process Efficiency with the Help of PolyWorks|Inspector™
Some of the most sought-after, high-end fabrication components for industries including automotive, heavy fabrication and construction equipment, off-road vehicles, and white goods are manufactured in the industrial town of Aurangabad in Maharashtra, India.

MetalMan Auto (P) Ltd. is one of the most reputed industrial organizations in Aurangabad. MetalMan’s visionary Director, Mr. Nishant Jairath, along with its Chief Operating Officer, Mr. Shrikant Mundada, have extensively managed the business for more than two decades. Their main plant at Aurangabad has been functioning under the leadership of Plant Head – Senior General Manager, Mr. Anilkumar Dahale.
The company is engaged in manufacturing sheet metal parts, tubular fabricated assemblies, and sub-assemblies for leading automotive OEMs. MetalMan makes use of a robust infrastructure including in-house surface treatment facilities, such as Nickel-Chromium (Ni-Cr) plating, cataphoresis electrolysis deposition (CED painting), epoxy powder coating and phosphating, as well as a dedicated CAD CAM and metrology setup.

The Challenge
In 2017, the company identified the need to speed up its inspection process. They were handling multiple projects and needed a faster turnaround while maintaining tolerances and accuracy.
Makarand Nikhade, Manager - QA, explains, “We supply parts to global OEMs from diverse industries. With every passing day, we see a change in customer expectations, especially in terms of the turnaround time and the output. To meet these demands, we needed software that could cut down our inspection time, provide us flexibility, and enhance output.”
Before opting for PolyWorks|Inspector, the company was using conventional inspection solutions that were time-consuming, resulting in operator fatigue. It also required only experienced metrology professionals as the system was complex.
“Our operator used to spend 6 to 7 hours to measure only one frame and generate the report. This was not only time-consuming but also difficult for operators,” adds Mr. Nikhade. “Since we had multiple plants and machines, streamlining inspecting operations was a daunting task.”
To summarize, the challenge was to find software that could offer speed but at the same time be easy to set up and use so that operators of various levels of experience could adapt quickly.
The Solution
“We purchased the first license of PolyWorks|Inspector in 2017 on a recommendation from Bajaj Auto (Indian automotive OEM). They were already using the software,” says the Quality Manager.
The MetalMan shop floor is equipped with all the latest manufacturing machines and solutions as they do not compromise on quality and speed. “It turned out to be a perfect match for our department, as we never shy away from investing in futuristic technologies. Our operators were also happy to see the functionality of the software,” he adds.
Kiran Pimple, Engineer QA, and operator of the software, agrees: “During the demo, I could see the difference it was going to bring to our inspection process. The software is highly intuitive and user-friendly. I believe the software design is very intelligent and allows me to make new projects in very little time.”
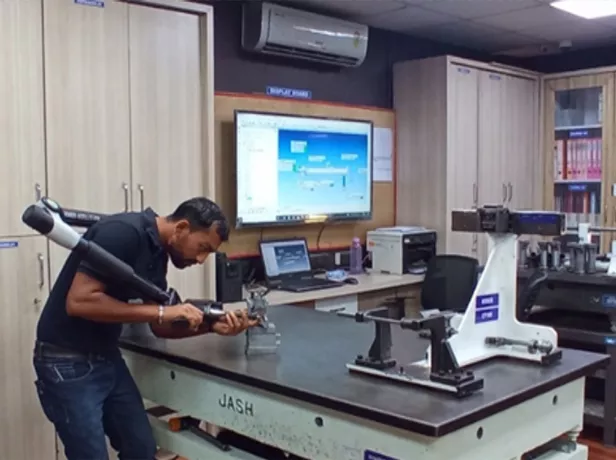
The Benefits
According to Mr. Nikhade, “What was important for us was to attain the accuracy to measure the frame/parts. The quantum is important, but quality is our priority, and this process had to be fast, yet easy to execute.”
MetalMan has been using PolyWorks|Inspector for more than six years in all its plants with 6 licenses purchased so far. Talking about the benefits, Kiran says, “We have CMMs of different makes and, with our earlier software, it was difficult to streamline all the reports. Since PolyWorks® supports all the CMMs and other measuring hardware, it has become easy for us to integrate inspection reports.”
“Since we use the tool for fabrication, this system gives us a very high speed of response to our customers when we probe or scan the parts and generate reports. With PolyWorks|Inspector, it only takes 45 minutes for us to analyze the part and generate a report, which would otherwise take 6 to 7 hours,” explains the Quality Manager.
Talking about the skills required for the software, the Quality Manager says, “Finding skilled labor is extremely difficult these days. However, the software is so user-friendly that a new operator who has basic engineering knowledge, but no prior experience can be trained within a few days. The software has helped us overcome this challenge. More than anything, it helped the operators and engineers become more confident about the correct dimensions of their product.”

MetalMan has some of the biggest and best in the business as customers, including Hero Moto Corp, TVS, Mahindra, Honda, Harley Davidson, Ashok Leyland, BMW, Volkswagen, SumiRiko, JCB, CNH, and Sonalika, among others.
They have also ventured into the world of EVs with their major customer being Gogoro from Taiwan, in addition to Ather Energy and Simple Energy. With a workforce of 1000+ skilled engineers equipped with the latest technologies, the company is well capable of handling challenging projects with ease.