Решение проблем протекания конструкции двери автомобиля
Компания Scanning and Inspection Pty обращается к PolyWorks® и анализирует взаимосвязь между дверной рамой и кузовом автомобиля менее чем за 1 час.
Производители знают, когда что-то идет не так, однако выяснение причин зачастую является гораздо более сложным процессом. Последующее расследование требует времени, денег и ресурсов. Даже после того, как проблема была окончательно выявлена, внесение количественных корректировок - это еще один этап на пути к исправлению ошибки. Иногда изготовленная деталь отличается от спроектированной или от того, какой она должна была быть или была в прошлом, но насколько, где и в каком направлении? Для крупного австралийского производителя автомобилей первоочередной задачей было выявление причины протекания дверных конструкций.

ModelMaker Z70, установленный на FaroArm
Задача
Производитель автомобилей недавно столкнулся с одним из этих неизбежных производственных сценариев. Они столкнулись с различиями в выравнивании некоторых уплотнителей дверей пассажирских салонов, которые они производили и собирали. Было очевидно, что некоторые автомобили, которые были произведены в течение одного определенного этапа производства, были такими, как ожидалось, двери и уплотнения находились в полном соответствии с остальной частью кузова автомобиля. Однако в тех, которые сходили с производственной линии на более позднем этапе, на этапе тестирования было обнаружено протекание воды. Первая задача заключалась в том, чтобы определить, куда проникает вода, но более сложный анализ касался взаимосвязи между дверной коробкой и кузовом автомобиля. Однако выяснение того, чем они отличаются от тех автомобилей, которые не протекали, и насколько, где и в каком направлении, было очень непросто.
Если одна партия автомобильных узлов вышла из производства и не имела проблем с протеканием, а другие, произведенные на более позднем этапе, протекали, то они должны как-то отличаться по своей структуре. Чем проблемный узел дверной коробки отличается от «хорошего»? Чтобы узнать, какие изменения необходимо внести во время производства, заказчик должен иметь возможность количественно оценить расхождение. Необходимо оценить взаимосвязь и различия между «хорошими» и «плохими» узлами дверной коробки. Был проведен подробный сравнительный анализ, и благодаря новейшим технологиям лазерного сканирования и пакету PolyWorks® он был выполнен в течение нескольких часов.
Решение
Получение данных
Чтобы быстро и эффективно собрать информацию о поверхности, специалисты Scanning and Inspection использовали лазерный сканер, установленный на измерительной руке. Для этого приложения использовался лазерный сканер ModelMaker Z70, высококачественный сканер, способный оцифровывать поверхность с поразительной плотностью 0,05 мм x 0,05 мм, что составляет около 400 точек на квадратный миллиметр. Это позволяет получить реалистичное и полное трехмерное цифровое представление детали, огромное количество данных, которые можно сразу преобразовать в полезную информацию. Сканер получает свою базовую 3D-модель от портативной КИМ, в данном случае Platinum FaroArm, которая измеряет повторяемость в пределах ± 0,0051 мм в зависимости от размера. FaroArm и лазерный сканер MMZ70 были перемещены на место с помощью сверхмощного штатива, поэтому оборудование можно было удобно установить рядом с дверьми автомобиля, которые требовалось проверить. Сбор необходимых данных о поверхности занял всего несколько минут на один автомобиль.
Процесс PolyWorks
После того как данные сканирования были собраны, начался этап пост-обработки. Используя PolyWorks, специалисты Scanning and Inspection Pty Ltd. виртуально сопоставили данные лазерного сканирования от «протекающего» автомобиля с данными «хорошего» автомобиля, а также выполнили расширенные измерения и сравнительный анализ. Однако перед проведением сравнительного анализа необходимо было провести серию манипуляций с облаком точек в PolyWorks.
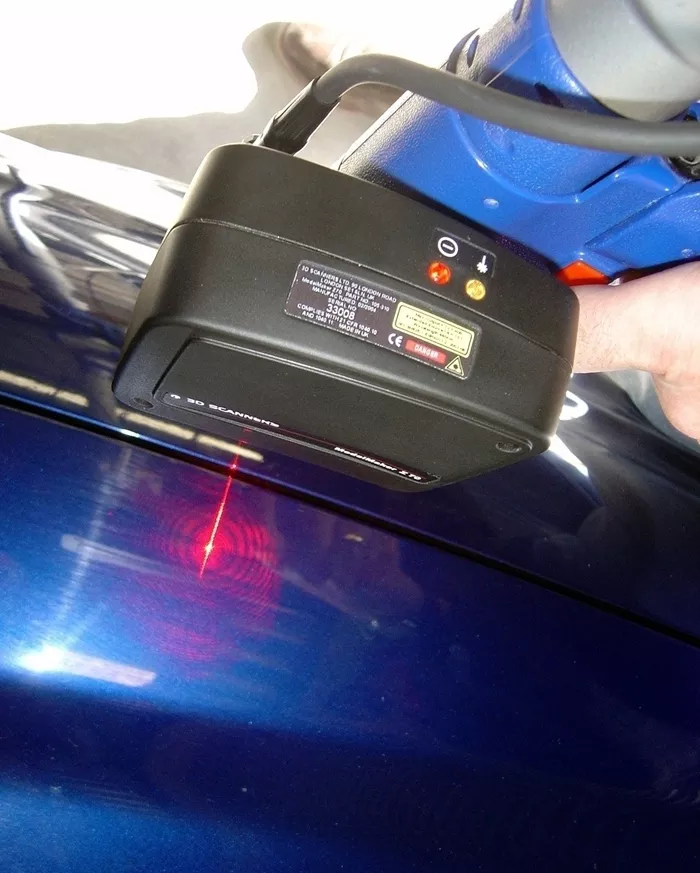
Получение данных
Уточнение выравнивания сканов
На этапе сбора данных было сделано несколько проходов сканирования. Каждый участок сканирования автоматически выравнивается с использованием собственной технологии выравнивания измерительной руки, которая обеспечивает пространственную привязку для меняющегося местоположения лазерного сканера. Большинство облаков точек, полученных лазерным сканером, «находятся» поверх других облаков, которые уже были учтены при других проходах сканера. Следовательно, некоторые части детали измеряются более одного раза. Эти области многоуровневых данных называются областями перекрытия.
Для уточнения выровненного облака точек, полученного с помощью портативной КИМ, модуль PolyWorks IMAlign использует эти области перекрытия для повторного выравнивания всех сканов. Сначала был проведен анализ отклонения выровненного облака точек. PolyWorks автоматически вычисляет средние расстояния между каждым перекрывающимся сканом и отображает цвет, который представляет значение отклонения. Пользователи могут с первого взгляда идентифицировать сканы, которые выходят за рамки допуска и могут быть улучшены путем повторного выравнивания.
Затем, используя метод «оптимального совмещения» PolyWorks, было выполнено повторное выравнивание. Чтобы предотвратить «смещение» между участками в одной и той же области, для каждого сканирования автоматически устанавливаются восемь контрольных точек, которые ограничивают степень свободы. Эта функция отличает PolyWorks от других решений для выравнивания сканов, при работе с которыми часто возникает проблема смещения во время выравнивания. После выполнения ограниченного выравнивания методом оптимального совмещения вычисляется новый анализ отклонений и отображается цветная карта.
Последний шаг заключается в создании однослойной модели облака точек путем интеллектуального усреднения всех перекрывающихся сканов с использованием технологии «уменьшения перекрытия» в PolyWorks. Получившееся облако точек теперь можно преобразовать в поверхность, которая будет использоваться для дальнейшего анализа, например, для сравнений отдельных дверей. Методология сканирования была одинаковой как для «протекающих», так и для «хороших» автомобилей. С рам окон и дверей была удалена вся периферийная отделка, чтобы обнажить только компоненты металлоконструкции этапа пост-производства. Двери были закрыты на протяжении всего процесса сбора данных, а соответствующие области, связанные с протекающими уплотнениями, сканировались с помощью лазера MMZ70.
По мере того как лазерная полоса перемещается по поверхности, собирая десятки тысяч трехмерных точек в секунду, следующая поверхность сразу же появляется на экране компьютера. Возможности такого отображения поверхности облака точек в реальном времени означали, что области, которые были пропущены или которые еще предстояло отсканировать, могли быть идентифицированы во время измерения и учтены соответствующим образом.

Создание полигональной модели
Создание полигональной модели
Чтобы сравнить поверхности «хороших» и «плохих» узлов дверной коробки, компании Scanning and Inspection требовалось преобразовать облака точек во что-то, что можно было использовать в качестве поверхности. PolyWorks мгновенно преобразовал десятки миллионов точек из облака точек в триангулированную сетку. Программа использовала каждую точку в качестве узлов для миллионов крошечных треугольников, которые она построила.
Чтобы точно описать различные формы отсканированного объекта, PolyWorks использует меньше треугольников для более согласованных участков поверхности автомобиля и больше треугольников, когда контур становится сложным, причем все это основано на значениях допуска, заданных пользователем. Перед преобразованием также задаются параметры «ближайшего соседа» и расстояния поиска, чтобы создать триангулированную поверхность и максимально снизить собственный шум цифрового преобразователя.
Сравнения дверей
Используя сложную серию математических вычислений по методу наименьших квадратов и поверхностного анализа, два только что триангулированных и оптимизированных набора данных лазерного сканирования были наложены один на другой и выровнены с использованием технологии оптимального совмещения PolyWorks. Затем программа PolyWorks разработала шаблон распределения с цветовой кодировкой, в которой сравниваются две конструкции. Полученная в результате цветная карта ошибок позволяет легко различить шаблоны, которые определяют, как «плохая» дверь автомобиля, в которой возникают протечки, соотносится с «хорошей» дверью.
Центральная стойка и нижние части дверей имеют светло-зеленый (почти аквамариновый) цвет, что указывает на отклонение между двумя комплектами дверей менее ± 0,5 мм. Другие области, такие как стальная оконная рама, приваренная к самой двери, показаны зеленым цветом, что соответствует отклонению ± 1-2 мм. Наконец, оранжевая секция, расположенная на шасси автомобиля, также указывает на отклонение ± 1-2 мм.
Другими словами, когда средние стойки двух автомобилей были выровнены с точностью до 0,5 мм, оконные рамы протекающего автомобиля фактически располагались на 0,5-2 мм ниже, чем у автомобиля, который не был подвержен протеканию, и этого, конечно, было достаточно для просачивания воды.
Преимущества
Инженеры Scanning and Inspection фактически обнаружили, что было бы намного проще изменить сварные швы, определяющие положение дверной коробки, чем каким-либо образом модифицировать шасси. Сварка в месте стыка оконной рамы с дверью была откорректирована таким образом, чтобы рама не сидела так низко (по сравнению с дверью, которая не протекала).
Весь процесс проверки PolyWorks был выполнен менее чем за час.
Выводы, сделанные в результате расследования, в основном касались проблем заказчика с оконной рамой автомобиля, или, в частности, способа ее приваривания к основной двери. Соответствующие корректировки были произведены в отношении сварочных операций, чтобы оконная рама больше не располагалась слишком глубоко внутри своего идеального положения, как указано в первоначальном проекте CAD.
Точность и гибкость FaroArm и лазерного сканера MMZ70, используемых в сочетании с программным обеспечением мирового класса PolyWorks, позволили этому автопроизводителю:
- Быстро определить источник протекания
- Точно измерить физическое отклонение «плохих» дверных узлов по сравнению с «хорошими» (насколько, где и в каком направлении)
- Модифицировать процесс сборки, отрегулировав сварку там, где оконная рама соединяется с дверью
- Выполнить весь процесс проверки менее чем за 1 час