Contracción, deformación y tiempo
InnovMetric y ShapeGrabber ayudan a MPC Molder a tomar decisiones de producción oportunas para piezas de automóviles.
A medida que los productos básicos de Miniature Precision Components (MPC) (es decir, válvulas de PCV, conectores, tuberías, accesorios, depósitos de fluidos, tapas de llenado, etc) se convirtieron en artículos básicos con márgenes de ganancia cada vez menores, MPC comenzó a ofrecer nuevos productos a los fabricantes de automóviles; entre ellos, cubiertas de motor adornadas con logotipos. A diferencia de casi toda la producción anterior de MPC, se trata de piezas muy estilizadas: abovedadas, en relieve o estriadas. Son lo que los fabricantes de automóviles llaman piezas “ornamentales”: los compradores en las salas de exhibición de los distribuidores las revisan.
Dado que estas piezas eran varias veces más grandes que casi todo lo que MPC había fabricado anteriormente, la contracción y la deformación representaban nuevos y complicados retos de garantía de calidad. Para comenzar la producción según lo planificado, los ingenieros se vieron obligados a tomar decisiones críticas sobre las herramientas y los procesos en muy poco tiempo y con muy pocos datos.
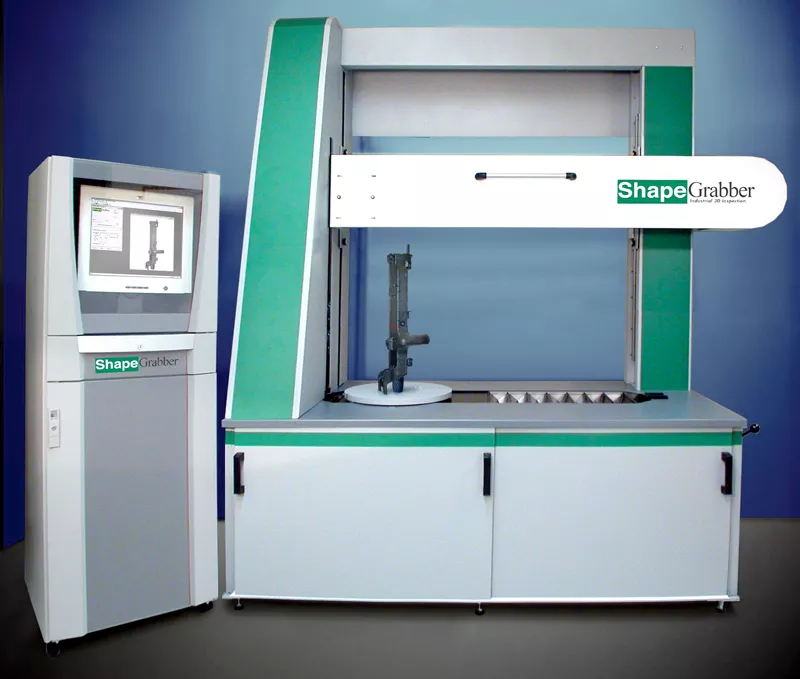
Por sí mismas, la contracción y la deformación pueden superar el límite de tolerancia total fácilmente. Las inevitables variaciones del proceso de moldeo hacen que las piezas se alejen aún más de las especificaciones. El tiempo es la esencia de la relación comercial, como siempre es el caso en la industria automotriz. MPC se da un plazo de solo cuatro semanas después de recibir un molde para comenzar la producción y entregar piezas de muestra.
Las dimensiones deben estar dentro de un límite de tolerancia de +/- 5 mm para adaptarse a todos los procesos, materiales y variaciones de herramientas.
La contracción y la deformación se resuelven:
- Cambiando el proceso de moldeo
- Relajando las tolerancias de la pieza
- Construyendo un accesorio de enfriamiento
- Modificando la herramienta que forma la pieza
Seleccionar e implementar cualquiera de estas opciones puede llevar tranquilamente cuatro semanas, con lo cual no queda tiempo para la resolución de problemas. “Cuatro semanas es el único plazo que tenemos para ajustar y estabilizar el proceso de moldeo”, dijo Clark, “y tenemos que cubrir mucho más que la contracción y la deformación.”
MPC resolvió sus problemas de contracción y deformación utilizando un escáner láser ShapeGrabber 3D y el software de inspección basado en nubes de puntos PolyWorks®, de InnovMetric Software. De una manera muy inteligente, la gerencia de MPC convirtió esta solución en un par de ventajas competitivas: Un menor tiempo de comercialización y una mayor garantía de calidad.
El reto
La gran dificultad que enfrentan los moldeadores con la contracción y la deformación es que se originan por causas distintas. La contracción está relacionada con el material; oscila entre el 2% y el 14% y puede variar en los diferentes lotes de resina. La deformación está relacionada con el enfriamiento y el uso de secciones gruesas y delgadas por parte del diseñador. Abordar satisfactoriamente estos retos dimensionales y de tolerancia requiere mucho análisis y cálculo, además de años de experiencia.
Los fabricantes de moldes empiezan a diseñar una nueva herramienta con valores de contracción estimados a partir de la hoja de datos de seguridad de materiales (MSDS) de la resina plástica. Para abordar la deformación, los fabricantes de moldes aplican sus conocimientos sobre conductos de entrada, ventilación y agua. Sin embargo, hasta que se construye y se utiliza una herramienta, la contracción y la deformación no son más que conjeturas fundamentadas.
El palpado táctil, el análisis de flujo del molde y la fotogrametría se quedaron cortos
Antes del escaneo láser y la inspección basada en nubes de puntos, los moldeadores no tenían herramientas de inspección de superficies que fueran completas y rápidas. Los mejores métodos disponibles eran el palpado táctil con una máquina de medición de coordenadas (CMM), el análisis del flujo del molde y la fotogrametría. Sin embargo, todos estos métodos se quedaron cortos.
Palpado táctil
El palpado táctil pasa por alto pequeñas protuberancias, ondulaciones y, como señaló Clark, “cosas más sutiles como un cambio por deformación en el tono de un par de puntos X y Y, lo que hace que otro punto quede fuera de su tolerancia Z.” Esta es la razón por la que inspeccionar minuciosamente una superficie requiere 500,000 puntos tridimensionales (3D) y, a veces, un millón o más, en lugar de los pocos cientos que ofrece un palpador táctil.
Además, agregó Clark, “la CMM tarda siete días hábiles en configurar un trabajo, dos días más en medir y otros cinco días después en procesar todos los datos. Debido a que la CMM siempre está ocupada, es posible que debamos esperar otros siete días para que llegue su turno en la cola. Entonces, con los métodos punto por punto, tenemos, en el mejor de los casos, solo dos oportunidades para hacerlo bien.”
Análisis de flujo de molde
El análisis de flujo del molde es una simulación por computadora que predice cómo se encogerá y deformará una resina según la ubicación y el tamaño de las compuertas de la herramienta. Hay tres grandes inconvenientes:
- Se utilizan dimensiones nominales en lugar de datos de inspección reales de la pieza; las subsecuentes revisiones de los moldes no pueden adaptarse fácilmente.
- Las predicciones de la deformación son únicamente teóricas y digitales. Ir más allá del ámbito virtual del flujo de moldes requiere refinamientos que los fabricantes de moldes pueden negarse a proporcionar.
- Como sucede con cualquier simulación, los análisis de flujo de molde contienen suposiciones implícitas y valores numéricos que pueden no ser válidos en el mundo real.
“Necesitamos saber lo que realmente sucedió en el molde y no lo que se suponía que iba a suceder”, dijo Clark. El análisis de flujo del molde también es costoso (hasta $12,000 por herramienta) y generalmente consume dos de las cuatro semanas programadas.
Fotogrametría
La fotogrametría es, literalmente, medir con fotografías de alta resolución. La fotogrametría captura superficies varias veces más grandes que las que capturan los escáneres láser, pero es posible que se requieran dianas pegadas para la alineación. Una vez que se digitalizan las fotos, se pueden comparar fácilmente con un archivo CAD descargado o se pueden cargar en un archivo CAD como un parche de superficie.
La fotogrametría se probó como una alternativa para verificar los accesorios y las galgas de los arneses de vacío del motor. “El problema de la inspección es que son diferentes para cada motor”, dijo Clark. “En los 13 años que he estado aquí, hemos comprado más de mil galgas que probablemente han costado $3.5 millones en total. Se trata de piezas negras, por lo que, al fotografiarse, no se logra obtener una buena imagen,” agregó, “y siempre tenemos problemas de luz ambiental y percepción de profundidad en el eje Z.”
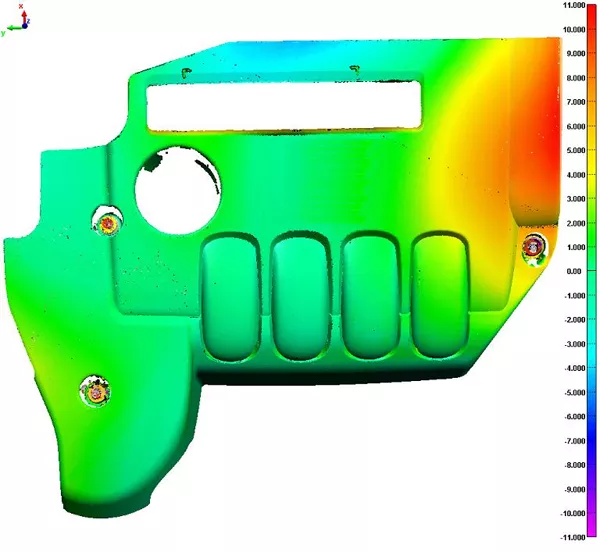
Mapa de color de comparación de datos a CAD
La solución
Para inspeccionar piezas de plástico, MPC utiliza el escáner ShapeGrabber Ai810C. Este escáner 3D de múltiples ejes permite al usuario solicitar un escaneo completo de la pieza con un solo clic del ratón: el sistema hace el resto.
Esta facilidad de uso se debe a la utilización de múltiples ejes de escaneo (horizontal y vertical), así como a un tercer eje rotativo sobre el que se coloca la pieza. Todos estos ejes se calibran en el mismo marco de referencia, de modo que múltiples escaneos se alinean automáticamente. Al configurar los escaneos necesarios para una pieza determinada con anticipación, todo el conjunto de escaneos se automatiza fácilmente.
El proceso de configuración toma solo unos minutos debido a la gran profundidad de campo (DOF) de los cabezales de escaneo. Esta gran DOF permite configurar los escaneos utilizando una interfaz de usuario gráfica sencilla e intuitiva, ya que no es necesario seguir de cerca el contorno complejo de la pieza como la mayoría de los otros escáneres.
Los cabezales de escaneo adquieren los datos a velocidades que varían entre 18,000 y 150,000 pts/s, por lo que solo se necesitan unos minutos para generar una nube de puntos completa que representa la pieza. Luego, PolyWorks|Inspector™ procesa fácilmente este archivo de datos para completar el proceso de inspección.
La combinación de velocidad y facilidad de uso del escáner hace que este sea accesible para un mayor número de usuarios y reduce el tiempo de configuración e inspección, con lo cual también se reduce drásticamente el costo de la inspección en comparación con los métodos alternativos.
Los datos que necesita MPC están disponibles en 15 minutos y no en días
Inspección basada en nubes de puntos en PolyWorks
Las inspecciones de la cubierta del motor de MPC ahora se realizan con mapas de tolerancias a todo color en PolyWorks|Inspector. PolyWorks compara millones de puntos de datos obtenidos por el escáner con el modelo CAD de referencia. Los especialistas de MPC establecen tolerancias en PolyWorks para determinar la desviación aceptable y no aceptable entre los puntos de datos y el modelo CAD. La pantalla utiliza todo el espectro de colores desde el rojo (tolerancias positivas, demasiado material) hasta el azul (tolerancias negativas, muy poco material). Debido a que la banda de tolerancia del mapa de color es ajustable, es una herramienta excelente para análisis hipotéticos. “Los mapas de color nos permiten ver lo que realmente está sucediendo dentro del molde, qué superficies se ven afectadas por el cambio de tolerancia y en qué medida”, explicó Clark. “Lo que realmente nos muestra el mapa de colores”, agregó, “es cómo la pieza de plástico flota dentro del molde. Sabemos que el material de la pieza se encogerá a sus dimensiones adecuadas y la deformación durante el enfriamiento le dará la forma que pidió su diseñador.”
Si los ingenieros de MPC necesitan verificar algo que no se especificó originalmente en el diseño de inspección, simplemente hacen clic en el punto en los datos o añaden puntos volviendo a escanear. En cualquier caso, es solo cuestión de minutos. Anteriormente, la CMM tenía que reprogramarse. “Para añadir incluso un solo punto de palpado táctil, teníamos que comenzar de nuevo”, dijo Clark. “Eso nunca toma menos de dos días.”
Para los usuarios de MPC y sus clientes, ShapeGrabber y PolyWorks era el único sistema que podía:
- Mantener el ritmo de las tasas de producción y las frecuencias de inspección
- Pasar las pruebas estándar de repetibilidad y reproducibilidad (R&R) que certifican los sistemas de inspección
En una prueba de R&R, un operador mide una entidad geométrica en 10 piezas tres veces. Luego, un segundo operador mide la misma entidad geométrica en las mismas 10 piezas tres veces más y se comparan los resultados. PolyWorks y ShapeGrabber pasaron satisfactoriamente las pruebas.
Todos los demás enfoques basados en láser fueron demasiado lentos. Ninguno de ellos pudo recopilar los datos necesarios en menos de dos o tres horas.
“En cuestión de minutos, en lugar de dos o tres semanas, el escaneo nos brinda todos los datos de superficie que necesitamos para elegir entre las opciones de producción”, dijo Clark. “Obtenemos la alineación y el formato gracias a PolyWorks casi en tiempo real. Finalmente, tenemos tiempo suficiente para tomar las decisiones difíciles de producción.” Agregó que, “Debido a que podemos recopilar todos los datos dimensionales y de tolerancia que necesitamos tan rápido, tenemos varios días más para diseñar y analizar cada trabajo. Ese tiempo adicional es de gran ayuda mientras decidimos si buscamos tolerancias más flexibles, modificamos la herramienta, cambiamos el proceso de alguna manera o hacemos que se fabrique un dispositivo de enfriamiento.”
El tiempo que se ahorra también significa que los ingenieros pueden regresar a revisar una vez más. Esto puede incluir áreas sospechosas en un nuevo lote de piezas de muestra. “ShapeGrabber y PolyWorks nos ayudan durante todo el proceso de configuración”, señaló Clark.
“Creemos que MPC logró un retorno de la inversión de dos semanas (R-O-I) con ShapeGrabber y PolyWorks”, agregó. “Nos han dado dos nuevas ventajas competitivas: garantía de calidad sin concesiones y un inicio rápido de la producción. Con el escaneo 3D y la inspección basada en nubes de puntos, ahora tenemos varios días adicionales para tomar decisiones importantes para los negocios. ShapeGrabber e InnovMetric nos han ayudado durante todo el proceso de configuración”, explicó Gregory Clark.
Los beneficios
Triunfar en un nuevo mercado exigente
La verdadera prueba de la eficacia de una nueva tecnología es si sus beneficios se extienden más allá de las necesidades de los usuarios en sus tareas diarias. En las grandes empresas, esos beneficios se manifiestan en inicios de producción más rápidos, más tiempo de ingeniería y análisis y mayor flexibilidad de métodos.
Esta solución ofreció:
- Garantía de mejor calidad, que ayuda a MPC a asegurarse de que las piezas se moldeen según se requiere, antes de enviar las muestras a los clientes.
- Eliminar numerosos controles dimensionales adicionales, lo cual permite que las herramientas y los procesos se cierrenmás pronto para la producción.
- Mayor flexibilidad de inspección, lo cual permite evaluar más opciones de producción y más tiempo para diseñar y probar moldes; esto se traduce directamente en la nueva ventaja competitiva de MPC, mejores piezas antes y clientes más satisfechos.
- Menor tiempo de comercialización, mientras la competencia pierde días o semanas en inspecciones con palpado táctil, MPC reúne entre 500,000 y más de un millón de puntos en una superficie en minutos.
- Una mayor capacidad para llegar a nuevos mercados. Con un salto adelante, MPC pasó de hacer piezas estrictamente funcionales y que no se ven frecuentemente a hacer cubiertas de motor muy estilizadas e idóneas para el comprador.
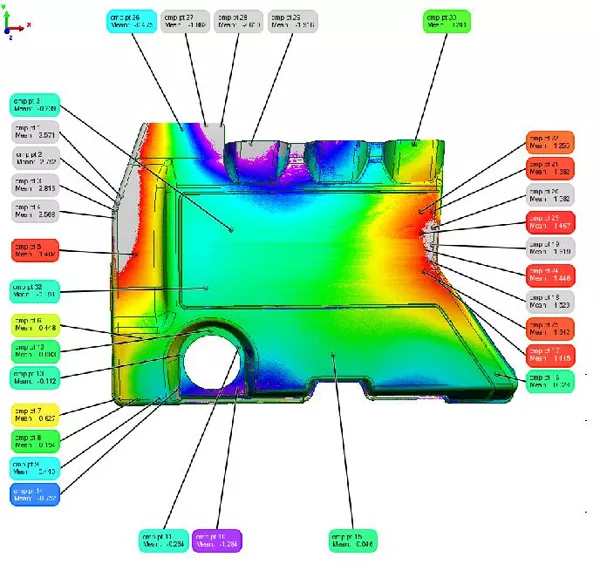