Ritiro, deformazione e tempo
InnovMetric e ShapeGrabber aiutano MPC Molder a prendere decisioni tempestive sulla produzione di ricambi automobilistici.
Dal momento che i prodotti di Miniature Precision Components (MPC) (vedasi valvole PCV, connettori, tubi, raccordi, serbatoi di fluidi, tappi di riempimento ecc.) sono diventati articoli di base con margini di profitto in calo, MPC ha iniziato a offrire nuovi prodotti alle case automobilistiche; tra questi figurano coperture per motori con l’applicazione di loghi. Diversamente da quasi tutta la produzione precedente di MPC, questi ultimi sono pezzi altamente caratterizzati da elementi stilistici: a cupola, in rilievo o scanalati. Sono ciò che le case automobilistiche chiamano componenti di “appearance”, ovvero elementi che gli acquirenti negli showroom dei concessionari osservano.
Dal momento che questi pezzi erano spesso molto più grandi di quasi tutto ciò che MPC aveva prodotto in precedenza, il ritiro e la deformazione presentavano nuove e difficili sfide in termini di garanzia della qualità. Per avviare la produzione entro i tempi previsti, gli ingegneri erano costretti a prendere decisioni critiche sugli strumenti e sui processi in tempi troppo brevi e con pochi dati.
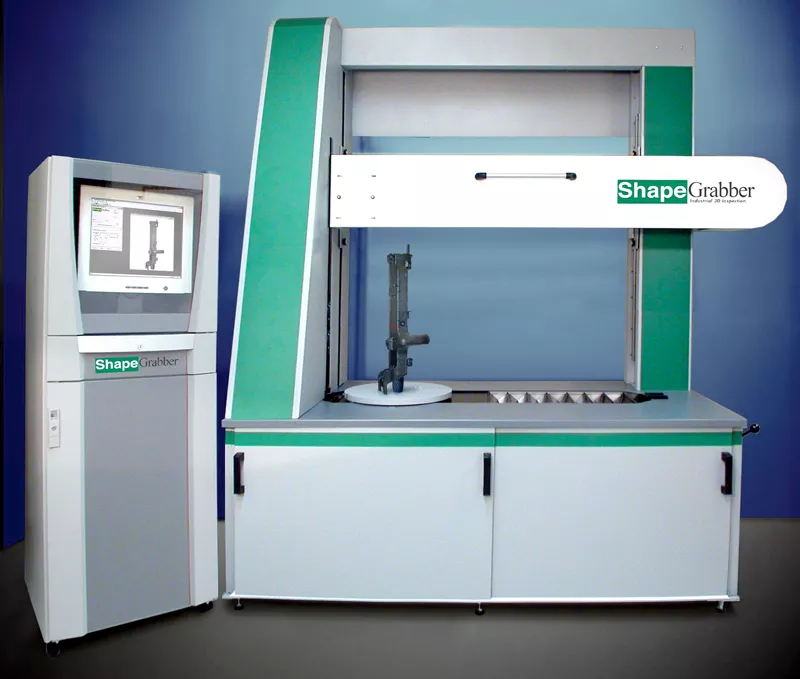
Di per sé, il restringimento e la deformazione sono aspetti che possono facilmente superare l'intero campo di tolleranza. Le inevitabili variazioni del processo di stampaggio allontanano i pezzi ancora di più dalle specifiche. Come è tipico delle case automobilistiche, il tempo è un aspetto essenziale del proprio business. MPC si concede solo quattro settimane dal ricevimento di uno stampo per avviare la produzione e inviare i pezzi campione.
Le dimensioni devono rientrare in un "budget" di tolleranza di +/- 5 mm per adattarsi a tutti i processi, i materiali e le variazioni degli utensili.
Il restringimento e la deformazione vengono gestiti:
- Modificando il processo di stampaggio
- Aumentando la permissività delle tolleranze del pezzo
- Costruendo un conformatore
- Modificando l'utensile che forma il pezzo
Selezionare e implementare una qualsiasi di queste soluzioni può richiedere facilmente quattro settimane, il che non lascia tempo per un'ulteriore risoluzione dei problemi. "Quattro settimane è l'unica finestra che abbiamo per modificare e stabilizzare il processo di stampaggio", spiega Clark, "e dobbiamo occuparci di molte altre cose oltre al restringimento e alla deformazione".
MPC ha risolto i suoi problemi di restringimento e deformazione utilizzando uno scanner laser 3D ShapeGrabber e il software di ispezione basato su nuvole di punti PolyWorks® di InnovMetric Software. Il management esperto di MPC ha trasformato la soluzione in alcuni vantaggi competitivi: Time to market ridotto e maggiore garanzia di qualità!
La sfida
La grande difficoltà che i costruttori di stampi devono affrontare con il restringimento e la deformazione è l’origine diversa delle cause. Il restringimento è legato al materiale; spazia tra il 2% e il 14% e può variare tra i diversi lotti di resina. La deformazione è correlata al raffreddamento e all'uso da parte del progettista sia di sezioni spesse che di sezioni sottili. Affrontare con successo queste sfide dimensionali e di tolleranza richiede molti calcoli e analisi oltre ad anni di esperienza.
I costruttori di stampi iniziano a progettare un nuovo utensile con valori di restringimento stimati a partire dalla scheda di sicurezza del materiale (MSDS) della resina plastica. Per affrontare la deformazione, i costruttori di stampi applicano la loro conoscenza di punti di ingresso, prese d'aria e linee idriche. Tuttavia, fino a quando un utensile non viene costruito e utilizzato, il restringimento e la deformazione sono solo ipotesi plausibili.
La tastatura, l'analisi del flusso di stampaggio e la fotogrammetria non erano all'altezza
Prima della scansione laser e dell'ispezione basata su nuvole di punti, i costruttori di stampi non disponevano di strumenti per l'ispezione delle superfici che fossero sia completi che rapidi. I migliori metodi disponibili erano la tastatura con una macchina di misura a coordinate (CMM), l'analisi del flusso di stampaggio e la fotogrammetria. Tuttavia, tutti questi metodi non erano all'altezza.
Tastatura
La tastatura non rileva piccole ammaccature, cedimenti e, come ha sottolineato Clark, "cose più sottili come uno spostamento di deformazione nel passo di una coppia di punti X e Y che porta un altro punto fuori dalla sua tolleranza Z". Questo è il motivo per cui l'ispezione approfondita di una superficie richiede 500.000 punti tridimensionali (3D) e talvolta un milione o più, anziché le poche centinaia fornite dal dispositivo di tastatura.
Inoltre, ha aggiunto Clark, “la CMM impiega sette giorni lavorativi per impostare un lavoro, altri due giorni per misurare e altri cinque giorni per analizzare tutti i dati. Dal momento che la CMM è sempre occupata, potrebbe essere necessario attendere altri sette giorni per avere un posto in coda. Quindi, con i metodi punto a punto, abbiamo al massimo solo due tentativi per farlo come si deve”.
Analisi del flusso di stampaggio
L'analisi del flusso di stampaggio è una simulazione al computer che prevede in che modo una resina si ritirerà e si deformerà in base alla posizione e alle dimensioni delle soglie dell'utensile. Esistono tre grandi svantaggi:
- Vengono utilizzate le dimensioni nominali anziché i dati di ispezione effettivi del pezzo; le successive revisioni dello stampo non possono essere facilmente inserite.
- Le previsioni di deformazione sono solo teoriche e digitali. Andare oltre il concetto virtuale del flusso di stampaggio richiede affinamenti che i produttori di stampi potrebbero rifiutarsi di fornire.
- Come ogni simulazione, anche le analisi del flusso di stampaggio contengono ipotesi implicite e valori numerici che potrebbero non reggere nel mondo reale.
“Ci serve sapere cosa è realmente accaduto nello stampo, non cosa sarebbe dovuto accadere”, ha spiegato Clark. Anche l'analisi del flusso di stampaggio è costosa, fino a 12.000 dollari a utensile, e di solito richiede due delle quattro settimane allocate.
Fotogrammetria
Fotogrammetria significa letteralmente misurare con la fotografia ad alta risoluzione. La fotogrammetria cattura superfici più grandi di molte volte rispetto a quelle degli scanner laser, ma per l'allineamento potrebbero essere necessari bersagli incollati. Una volta digitalizzate, le foto possono essere prontamente confrontate con un file CAD scaricato o possono essere caricate su un file CAD come patch di superficie.
La fotogrammetria è stata provata come alternativa per controllare le fixture e i calibri per le cinghie di vuoto dei motori. "Il problema dell'ispezione è che sono diverse per ciascun motore", ha spiegato Clark. “Nei 13 anni in cui sono stato qui, abbiamo acquistato oltre un migliaio di calibri che probabilmente costano un totale di 3,5 milioni di dollari. Sono parti di colore nero, quindi si fotografano male o affatto", ha aggiunto, "e abbiamo sempre problemi di luce ambientale e di percezione della profondità nell'asse Z”.
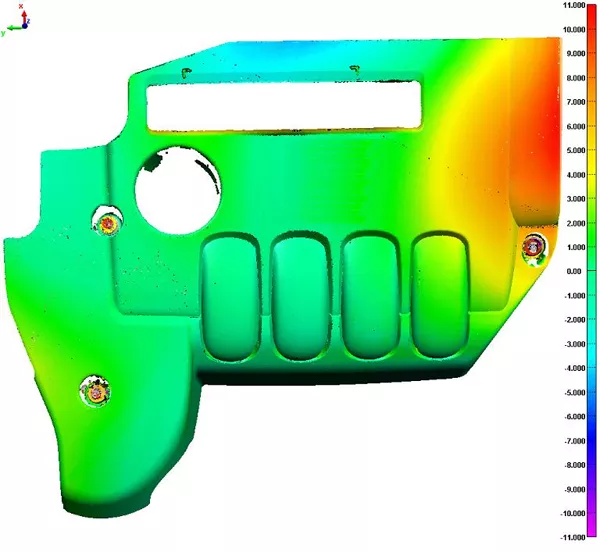
Confronto dati-CAD con mappa di colori
La soluzione
Per ispezionare parti in plastica, MPC utilizza lo scanner ShapeGrabber Ai810C. Questo scanner 3D multi-asse consente all'utente di richiedere una scansione completa del pezzo con un solo clic del mouse: il sistema fa il resto.
Questa facilità d'uso è dovuta all’impiego di più assi di scansione (orizzontale e verticale) e di un terzo asse rotante su cui viene posizionato il pezzo. Tutti questi assi sono calibrati nello stesso sistema di riferimento, in modo tale che più scansioni vengano allineate automaticamente. Impostando in anticipo le scansioni richieste per un dato pezzo, il set completo di scansioni viene facilmente automatizzato.
Il processo di configurazione richiede solo pochi minuti data l'elevata profondità di campo (DOF) delle teste di scansione. Questa DOF elevata consente di impostare le scansioni utilizzando un'interfaccia utente grafica semplice e intuitiva, dal momento che non è necessario seguire da vicino il complesso contorno del pezzo come nella maggior parte degli altri scanner.
Le teste di scansione acquisiscono i dati a velocità comprese tra 18.000 e 150.000 punti/s, in modo tale che bastino pochi minuti per generare una nuvola di punti completa che rappresenta il pezzo. Questo file di dati viene quindi facilmente elaborato da PolyWorks|Inspector™ per completare il processo di ispezione.
La combinazione di velocità e facilità d’uso rende lo scanner accessibile a un numero maggiore di utenti, e riduce i tempi di configurazione e ispezione, diminuendo drasticamente i costi di ispezione rispetto ai metodi alternativi.
I dati di cui ha bisogno MPC sono disponibili in 15 minuti, anziché in giorni
Ispezione basata su nuvole di punti in PolyWorks
Le ispezioni delle calotte dei motori presso MPC vengono ora eseguite con mappe delle tolleranze a colori in PolyWorks|Inspector. PolyWorks confronta milioni di punti di dati ottenuti dallo scanner con il modello CAD di riferimento. Gli specialisti di MPC impostano le tolleranze in PolyWorks per determinare la deviazione accettabile e non accettabile tra i punti di dati e il modello CAD. Il display utilizza l'intero spettro di colori dal rosso (, eccesso di materiale) al blu (, mancanza di materiale). Dal momento che la banda di tolleranza della mappa di colori è regolabile, si rivela uno strumento eccellente per le analisi what-if. “Le mappe di colori ci permettono di vedere cosa sta realmente accadendo all'interno dello stampo, quali superfici sono interessate dal cambiamento di una tolleranza, e quanto”, ha spiegato Clark. "Ciò che la mappa di colori ci mostra veramente”, ha aggiunto, "è come il particolare in plastica fluttua all'interno dello stampo. Sappiamo che il materiale del pezzo si restringerà nelle sue giuste dimensioni e la deformazione durante il raffreddamento lo porterà nella forma richiesta dal suo progettista”.
Se gli ingegneri MPC devono controllare qualcosa di non originariamente specificato nel layout dell’ispezione, fanno semplicemente clic sul punto nei dati o aggiungono punti mediante una nuova scansione. In entrambi i casi, è solo questione di minuti. In passato era necessario riprogrammare la CMM. “Per aggiungere anche un singolo punto di tastatura, bisognava ricominciare tutto dall’inizio”, ha spiegato Clark. “Servono sempre almeno due giorni”.
Per gli utenti di MPC e i suoi clienti, il sistema ShapeGrabber e PolyWorks è stato l'unico in grado di:
- Tenere il passo con i ritmi di produzione e le frequenze di ispezione
- Superare i test di ripetibilità e riproducibilità (R&R) standard che certificano i sistemi di ispezione
In un test R&R, un operatore misura una caratteristica su 10 pezzi tre volte. Quindi un secondo operatore misura la stessa caratteristica sugli stessi 10 pezzi altre tre volte e i risultati vengono confrontati. PolyWorks e ShapeGrabber hanno superato con successo questi test.
Qualsiasi altro approccio basato sul laser era troppo lento. Nessuno riusciva a raccogliere i dati necessari in meno di due o tre ore.
“In pochi minuti, anziché due o tre settimane, la scansione ci fornisce tutti i dati sulle superfici di cui abbiamo bisogno per scegliere tra le opzioni di produzione”, ha spiegato Clark. “Otteniamo l'allineamento e la formattazione da PolyWorks quasi in tempo reale. Abbiamo quindi tempo a sufficienza per prendere le difficili decisioni sulla produzione”. Ha aggiunto: “Dal momento che è possibile raccogliere tutti i dati dimensionali e di tolleranza di cui abbiamo bisogno così rapidamente, possiamo disporre di diversi giorni aggiuntivi per progettare e analizzare ciascun lavoro. Questo tempo extra è di grande aiuto nel momento in cui si deve decidere se cercare tolleranze più larghe, modificare l’utensile, cambiare il processo in qualche modo o far realizzare un conformatore”.
Il tempo guadagnato consente anche agli ingegneri di tornare indietro per dare una seconda occhiata, per individuare, ad esempio, aree sospette in un nuovo lotto di campioni. “ShapeGrabber e PolyWorks ci aiutano nell'intero processo di configurazione”, ha osservato Clark.
“Riteniamo che MPC abbia ottenuto un ritorno sull'investimento (ROI) di due settimane con ShapeGrabber e PolyWorks”, ha aggiunto. “Ci hanno fornito due nuovi vantaggi competitivi: garanzia di qualità senza compromessi e avvio rapido della produzione. Grazie alla scansione 3D e all'ispezione basata su nuvole di punti, ora disponiamo di diversi giorni aggiuntivi per prendere decisioni commerciali critiche. “ShapeGrabber e InnovMetric ci hanno aiutato nell'intero processo di configurazione”, ha spiegato Gregory Clark.
Vantaggi
Vincere in un nuovo mercato esigente
La vera prova di efficacia di una nuova tecnologia si vede quando i suoi vantaggi vanno oltre le esigenze degli utenti nelle loro attività quotidiane. Nelle imprese più grandi, questi vantaggi si traducono in tempi più rapidi per la produzione, più tempo da dedicare alla progettazione e all’analisi e una maggiore flessibilità dei metodi.
Questa soluzione ha offerto:
- Più garanzia di qualità, che aiuta MPC ad assicurarsi che i particolari vengano stampati come richiesto, prima che i campioni vengano inviati ai clienti.
- La possibilità di eliminare numerosi controlli dimensionali aggiuntivi, consentendo una gestione più efficiente delle attrezzature e dei processi per la produzione.
- Maggiore flessibilità nell’ispezione, che consente di valutare più opzioni di produzione e offre più tempo per la progettazione e il collaudo degli stampi; questo si traduce direttamente nel nuovo vantaggio competitivo di MPC: pezzi migliori realizzati in anticipo e clienti più soddisfatti.
- Tempi di immissione sul mercato ridotti: mentre i concorrenti perdono giorni o settimane con le ispezioni basate sulla tastatura a contatto, MPC raccoglie da 500.000 a un milione di punti su una superficie in pochi minuti.
- Una maggiore capacità di accedere a nuovi mercati. MPC è passato dalla produzione di pezzi strettamente funzionali e praticamente invisibili a coperture per motori caratterizzati da elementi stilistici e quindi altamente visibili.
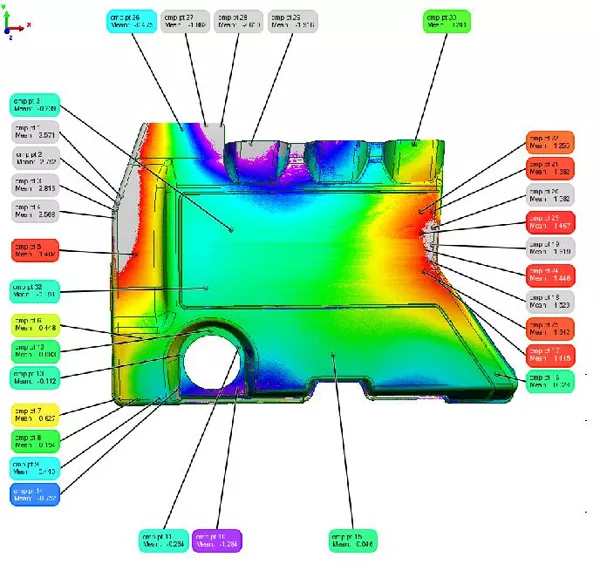