Schrumpfung, Verzug und Zeit
InnovMetric und ShapeGrabber helfen MPC Molder, zeitnahe Produktionsentscheidungen für Autoteile zu treffen.
Da die Brot-und-Butter-Produkte von Miniature Precision Components (MPC) (d.h. PCV-Ventile, Anschlüsse, Schläuche, Beschläge, Flüssigkeitsbehälter, Tankdeckel usw.) zu Massenware mit schrumpfenden Gewinnspannen wurden, begann MPC, den Automobilherstellern neue Produkte anzubieten; dazu gehören Motorabdeckungen mit Logoaufdruck. Im Gegensatz zu fast allen früheren MPC-Produkten handelt es sich hier um stark geformte Teile: gewölbt, geprägt oder geriffelt. Sie sind das, was die Automobilhersteller als „sichtbare“-Teile bezeichnen: Käufer in den Ausstellungsräumen der Händler sehen sie sich an.
Da diese Teile um ein Vielfaches größer waren als fast alles, was MPC zuvor hergestellt hatte, stellten Schrumpfung und Verzug neue und schwierige Herausforderungen für die Qualitätssicherung dar. Um die Produktion termingerecht zu starten, waren die Ingenieure gezwungen, in zu kurzer Zeit und mit zu wenigen Daten kritische Werkzeug- und Prozessentscheidungen zu treffen.
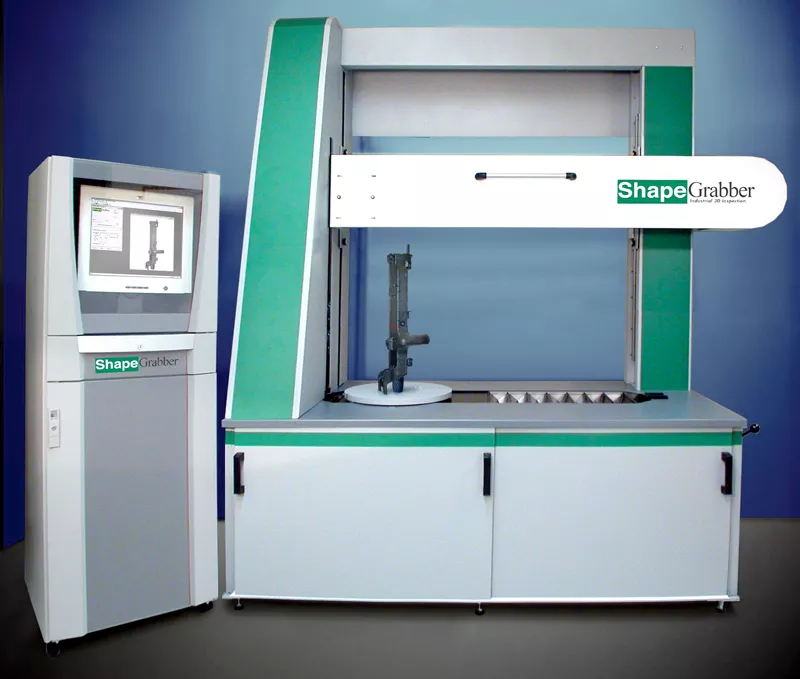
Schrumpfung und Verzug können für sich genommen leicht das gesamte Toleranzbudget überschreiten. Die unvermeidlichen Schwankungen im Gießprozess führen dazu, dass die Teile noch weiter von den Spezifikationen abweichen. Wie immer bei den Automobilherstellern ist die Zeit das A und O einer Geschäftsbeziehung. MPC lässt sich nur vier Wochen nach Erhalt einer Form Zeit, um mit der Produktion zu beginnen und Musterteile vorzulegen.
Die Abmessungen müssen innerhalb eines „Toleranzbudgets“ von +/- 5 mm liegen, um alle Prozesse, Materialien und Werkzeugabweichungen zu berücksichtigen.
Schrumpfung und Verzug werden behandelt durch:
- Änderung des Formgebungsverfahrens
- Lockerung der Toleranzen für das Teil
- Bau einer Kühlvorrichtung
- Ändern des Werkzeugs, welches das Teil formt
Die Auswahl und Implementierung einer dieser Lösungen kann leicht vier Wochen in Anspruch nehmen, so dass keine Zeit für die weitere Fehlersuche bleibt. „Vier Wochen sind das einzige Zeitfenster, das uns zur Verfügung steht, um den Formgebungsprozess zu optimieren und zu stabilisieren“, so Clark, „und wir müssen viel mehr als nur Schrumpfung und Verzug berücksichtigen.“
MPC löste seine Schrumpf- und Verzugsprobleme mit einem ShapeGrabber 3D-Laserscanner und der punktwolkenbasierten Prüfsoftware PolyWorks® von InnovMetric Software. Ein kluges MPC-Management verwandelte die Lösung in zwei Wettbewerbsvorteile: Kürzere Markteinführungszeiten und ein höheres Maß an Qualitätssicherung!
Die Herausforderung
Die große Schwierigkeit, die sich den Spritzgießern bei Schrumpfung und Verzug stellt, besteht darin, dass sie unterschiedliche Ursachen haben. Die Schrumpfung ist materialbedingt; sie liegt zwischen 2 % und 14 % und kann zwischen den einzelnen Harzchargen variieren. Der Verzug hängt mit der Kühlung und der Verwendung von dicken und dünnen Profilen durch den Konstrukteur zusammen. Die erfolgreiche Bewältigung dieser Herausforderungen in Bezug auf Abmessungen und Toleranzen erfordert eine Menge Analysen und Berechnungen sowie jahrelange Erfahrung.
Formenbauer beginnen die Konstruktion eines neuen Werkzeugs mit geschätzten Schrumpfungswerten aus dem Sicherheitsdatenblatt (MSDS) des Kunststoffs. Um dem Verzug zu begegnen, wenden die Formenbauer ihr Wissen über Anschnitte, Entlüftungen und Wasserleitungen an. Solange ein Werkzeug jedoch nicht gebaut und in Betrieb ist, sind Schrumpfung und Verzug nur Vermutungen.
Antasten, Mold-Flow-Analyse und Photogrammetrie waren nicht ausreichend
Vor der Einführung des Laserscannings und der punktwolkenbasierten Inspektion verfügten die Gießer über keine umfassenden und schnellen Werkzeuge für die Oberflächeninspektion. Die besten verfügbaren Methoden waren die Antastung mit einem Koordinatenmessgerät (KMG), die Mold-Flow-Analyse und die Photogrammetrie. Diese Methoden waren jedoch allesamt unzureichend.
Antasten
Beim Antasten werden winzige Unebenheiten, Durchbiegungen und, wie Clark betonte, „subtilere Dinge wie eine Verformungsverschiebung in der Neigung eines Paares von X- und Y-Punkten, die einen anderen Punkt aus seiner Z-Toleranz verdreht“, übersehen Aus diesem Grund sind für die gründliche Prüfung einer Oberfläche 500.000 dreidimensionale (3D) Punkte erforderlich, manchmal sogar eine Million oder mehr, und nicht nur ein paar Hundert, wie es bei der Abtastung der Fall ist.
Außerdem, so Clark, „benötigt das KMG sieben Arbeitstage für die Einrichtung eines Auftrags, zwei weitere Tage für die Messung und danach weitere fünf Tage für die Auswertung aller Daten. Da das KMG immer besetzt ist, müssen wir möglicherweise weitere sieben Tage warten, um einen Platz in der Warteschlange zu bekommen. Bei der Punkt-für-Punkt-Methode haben wir also bestenfalls zwei Versuche, um es richtig zu machen.“
Mold-Flow-Analyse
Bei der Mold-Flow-Analyse handelt es sich um eine Computersimulation, die vorhersagt, wie ein Kunststoff auf der Grundlage der Lage und Größe der Anschnitte des Werkzeugs schrumpfen und sich verziehen wird. Es gibt drei große Nachteile:
- Es werden Sollmaße und nicht die tatsächlichen Prüfdaten des Teils verwendet; spätere Formänderungen können nicht ohne weiteres berücksichtigt werden.
- Vorhersagen über den Verzug sind nur theoretisch und digital. Um über die virtuelle Welt des Mold-Flow hinauszugehen, sind Verbesserungen erforderlich, die die Formenbauer möglicherweise nicht bereitstellen.
- Wie jede Simulation enthalten auch Mold-Flow-Analysen implizite Annahmen und numerische Werte, die in der realen Welt möglicherweise nicht zutreffen.
„Wir müssen wissen, was in der Form tatsächlich passiert ist und nicht, was eigentlich passieren sollte“, sagte Clark. Die Mold-Flow-Analyse ist ebenfalls kostspielig – bis zu 12.000 Dollar pro Werkzeug – und nimmt in der Regel zwei der vorgesehenen vier Wochen in Anspruch.
Photogrammetrie
Photogrammetrie ist buchstäblich Vermessung mit hochauflösender Fotografie. Die Photogrammetrie erfasst Oberflächen, die um ein Vielfaches größer sind als die von Laserscannern, aber für die Ausrichtung sind unter Umständen aufgeklebte Ziele erforderlich. Sobald die Fotos digitalisiert sind, können sie leicht mit einer heruntergeladenen CAD-Datei verglichen oder als Oberflächenpatch in eine CAD-Datei hochgeladen werden.
Die Photogrammetrie wurde als Alternative zu Prüfvorrichtungen und Messgeräten für Motorunterdruckkabelbäume getestet. „Das Problem bei der Inspektion ist, dass sie für jeden Motor unterschiedlich sind“, so Clark. „In den 13 Jahren, in denen ich hier bin, haben wir über tausend Messgeräte gekauft, die wahrscheinlich insgesamt 3,5 Millionen Dollar gekostet haben. Da es sich um schwarze Teile handelt, lassen sie sich schlecht oder gar nicht fotografieren“, fügte er hinzu, „und wir haben immer Probleme mit dem Umgebungslicht und der Tiefenwahrnehmung in der Z-Achse.“
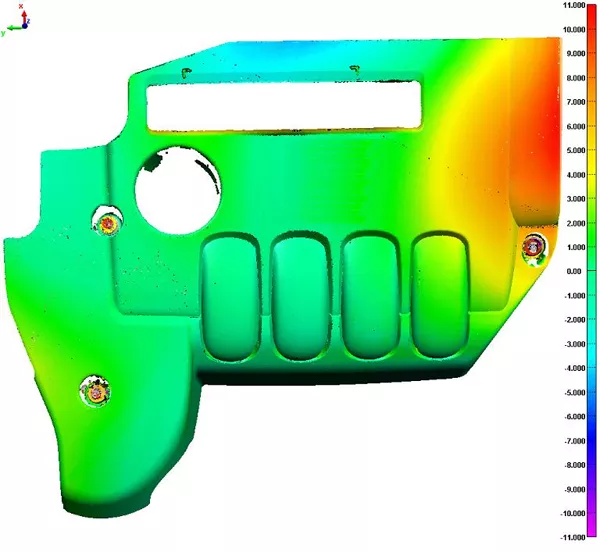
Farbkarte des Daten-CAD-Vergleichs
Die Lösung
Zur Prüfung von Kunststoffteilen verwendet MPC den Scanner ShapeGrabber Ai810C. Mit diesem mehrachsigen 3D-Scanner kann der Benutzer mit einem einzigen Mausklick einen kompletten Teilescan anfordern: Das System erledigt den Rest.
Diese Benutzerfreundlichkeit ist auf die Verwendung mehrerer Scan-Achsen (horizontal und vertikal) sowie einer dritten Drehachse zurückzuführen, auf der das Teil platziert wird. Alle diese Achsen werden auf denselben Referenzrahmen kalibriert, so dass mehrere Scans automatisch ausgerichtet werden. Indem man die erforderlichen Scans für ein bestimmtes Teil im Voraus einrichtet, lässt sich der gesamte Scan-Satz leicht automatisieren.
Aufgrund der sehr großen Schärfentiefe (DOF) der Scanköpfe dauert der Einrichtungsprozess nur wenige Minuten. Diese große DOF ermöglicht die Einrichtung der Scans über eine einfache und intuitive grafische Benutzeroberfläche, da es nicht notwendig ist, die komplexe Kontur des Teils genau zu verfolgen, wie bei den meisten anderen Scannern.
Die Scanköpfe erfassen die Daten mit Geschwindigkeiten zwischen 18.000 und 150.000 Punkten pro Sekunde, so dass es nur wenige Minuten dauert, eine vollständige Punktwolke des Teils zu erstellen. Diese Datei kann dann von PolyWorks|Inspector™ problemlos verarbeitet werden, um den Prüfprozess abzuschließen.
Die Kombination aus Geschwindigkeit und Benutzerfreundlichkeit des Scanners macht den Scanner für eine größere Anzahl von Benutzern zugänglich und reduziert die Einrichtungs- und Prüfzeit, wodurch die Prüfkosten im Vergleich zu alternativen Methoden drastisch gesenkt werden.
Die Daten, die MPC benötigt, sind in 15 Minuten verfügbar – statt in Tagen
Punktwolkenbasierte Inspektion in PolyWorks
MPCs Motorabdeckungsinspektionen werden jetzt mit vollfarbigen Toleranzkarten in PolyWorks|Inspector durchgeführt. PolyWorks vergleicht Millionen von Datenpunkten des Scanners mit dem CAD-Referenzmodell. MPC-Spezialisten legen in PolyWorks Toleranzen fest, um die akzeptablen und nicht akzeptablen Abweichungen zwischen Datenpunkten und CAD-Modell zu bestimmen. Die Anzeige nutzt das gesamte Farbspektrum von Rot (Plus-Toleranz, zu viel Material) bis Blau (Minus-Toleranz, zu wenig Material). Da das Toleranzband der Farbkarte anpassbar ist, ist sie ein hervorragendes Werkzeug für Was-wäre-wenn-Analysen. „Anhand der Farbkarten können wir sehen, was wirklich im Inneren der Form vor sich geht und welche Oberflächen in welchem Maße von der Änderung einer Toleranz betroffen sind“, erklärt Clark. „Was uns die Farbkarte wirklich zeigt“, fügte er hinzu, „ist, wie das Kunststoffteil in der Form schwimmt. Wir wissen, dass das Material des Teils auf die richtigen Maße schrumpft und die Verformung während des Abkühlens es in die Form bringt, die der Konstrukteur gewünscht hat.“
Wenn MPC-Ingenieure etwas prüfen müssen, das ursprünglich nicht im Prüfplan angegeben war, klicken sie einfach auf den Punkt in den Daten oder fügen Punkte durch erneutes Scannen hinzu. In jedem Fall ist es nur eine Frage von Minuten. In der Vergangenheit musste das KMG umprogrammiert werden. „Um auch nur einen einzigen berührungsempfindlichen Punkt hinzuzufügen, musste man ganz von vorne anfangen“, so Clark. „Das dauert nie weniger als zwei Tage.“
Für die Anwender bei MPC und deren Kunden war ShapeGrabber und PolyWorks das einzige System, das dies konnte:
- Mit den Produktionsraten und der Häufigkeit der Kontrollen Schritt halten
- Bestehen Sie die Standardtests zur Wiederholbarkeit und Reproduzierbarkeit (R&R), mit denen Prüfsysteme zertifiziert werden
Bei einem R&R-Test misst ein Bediener ein Merkmal an 10 Teilen dreimal. Dann misst ein zweiter Bediener dasselbe Merkmal an denselben 10 Teilen drei weitere Male und die Ergebnisse werden verglichen. PolyWorks und ShapeGrabber haben diese Tests erfolgreich bestanden.
Alle anderen laserbasierten Verfahren waren viel zu langsam. Keiner von ihnen konnte die erforderlichen Daten in weniger als zwei oder drei Stunden erfassen.
„Innerhalb von Minuten, anstatt von zwei oder drei Wochen, erhalten wir durch das Scannen alle Oberflächendaten, die wir für die Auswahl der Produktionsoptionen benötigen“, so Clark. „Wir erhalten die Ausrichtung und Formatierung von PolyWorks nahezu in Echtzeit. Endlich haben wir genug Zeit, um die schwierigen Produktionsentscheidungen zu treffen.“ Er fügte hinzu: „Da wir alle benötigten Maß- und Toleranzdaten so schnell erfassen können, haben wir mehrere zusätzliche Tage Zeit, um jeden Auftrag zu planen und zu analysieren. Diese zusätzliche Zeit ist eine große Hilfe bei der Entscheidung, ob wir engere Toleranzen anstreben, das Werkzeug modifizieren, den Prozess in irgendeiner Weise ändern oder eine Kühlvorrichtung anfertigen lassen sollen.“
Die gewonnene Zeit ermöglicht es den Ingenieuren auch, einen zweiten Blick darauf zu werfen. Dazu können auch verdächtige Bereiche in einer neuen Charge von Musterteilen gehören. „ShapeGrabber und PolyWorks unterstützen uns während des gesamten Einrichtungsprozesses“, so Clark.
„Wir glauben, dass MPC mit ShapeGrabber und PolyWorks einen Return on Investment (R-O-I) von zwei Wochen erreicht hat“, fügt er hinzu. „Sie haben uns zwei neue Wettbewerbsvorteile verschafft: kompromisslose Qualitätssicherung und schneller Produktionsstart. Mit 3D-Scans und punktwolkenbasierten Inspektionen haben wir jetzt mehrere Tage mehr Zeit, um wichtige Geschäftsentscheidungen zu treffen. ShapeGrabber und InnovMetric haben uns während des gesamten Einrichtungsprozesses geholfen“, erklärt Gregory Clark.
Die Vorteile
Erfolgreich auf einem anspruchsvollen neuen Markt
Der eigentliche Test für die Wirksamkeit einer neuen Technologie ist, ob ihr Nutzen über die Bedürfnisse der Nutzer bei ihren täglichen Aufgaben hinausgeht. In größeren Unternehmen zeigen sich diese Vorteile in einem schnelleren Produktionsstart, mehr Zeit für Entwicklung und Analyse und einer größeren Flexibilität der Methoden.
Diese Lösung wurde angeboten:
- Verbesserte Qualitätssicherung, mit der MPC sicherstellen kann, dass die Teile wie gewünscht geformt werden, bevor die Muster an die Kunden geschickt werden.
- Es entfallen zahlreiche zusätzliche Maßprüfungen, so dass Werkzeuge und Prozesse schneller für die Produktion bereitgestellt werden können.
- Erhöhte Flexibilität bei der Inspektion, wodurch mehr Produktionsoptionen evaluiert werden können und mehr Zeit für den Entwurf und die Erprobung von Formen zur Verfügung steht; dies führt direkt zu einem neuen Wettbewerbsvorteil von MPC – bessere Teile in kürzerer Zeit und zufriedenere Kunden.
- Verkürzte Markteinführungszeit: Während die Konkurrenz Tage oder Wochen mit Antastinspektionen vergeudet, erfasst MPC innerhalb von Minuten 500.000 bis über eine Million Punkte auf einer Oberfläche.
- Eine verbesserte Fähigkeit, neue Märkte zu erschließen. MPC hat sich mit einem Sprung von rein funktionalen, selten zu sehenden Teilen zu hochgradig stilisierten Motorabdeckungen entwickelt, die dem Käufer direkt ins Auge springen.
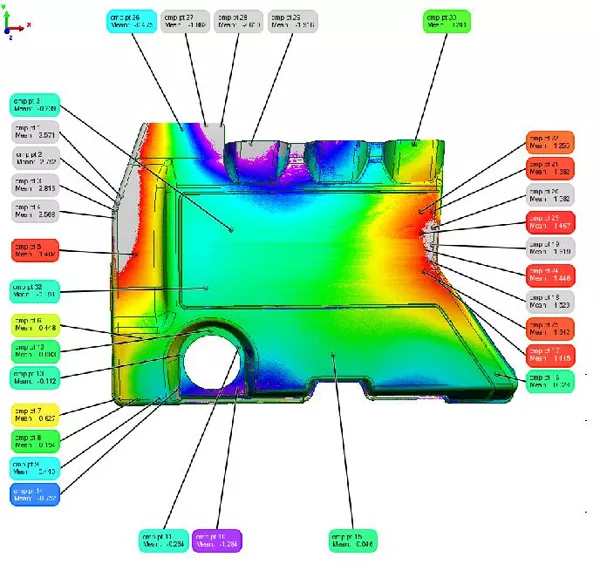